"F1 is really a battle of technologies, and the best technology wins the race." - Nika Lauda
Formula 1 is a sport cloaked in mystery and high-stakes engineering. The cars, sleek and powerful, are the result of thousands of hours in design, testing, and research & development. It might seem like magic goes into car development, but beneath the layers of secrecy are fundamentals that anyone can understand!
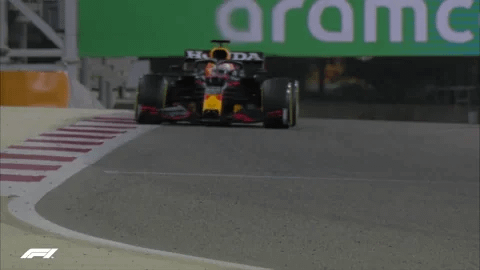
The motor sport has seen a massive surge in popularity in recent years from the Netflix series "Drive to Survive". By revealing the personal stories, fierce rivalries, and behind-the-scenes drama, it’s drawn in a new wave of fans who might have otherwise never paid attention to what happens on the racetrack.
Understanding the basics of Formula 1 engineering doesn’t mean you’ll uncover the teams’ closely guarded secrets. But it does mean you’ll appreciate the ingenuity that goes into every car.
In part one of this installment, we’ll focus on the history and evolution of F1 cars, car design (aerodynamics, tire fundamentals, etc.), and development cycles for Formula 1 cars.
History and Evolution of Formula 1 Cars
Formula One has always been about one thing: the relentless pursuit of speed. From running on foot to riding horses and eventually to racing cars, the essence of the race hasn't changed: get from start to finish as quickly as possible. Formula One is the pinnacle of this fascination.
Over the decades since the inception of Formula One by the FIA (Fédération Internationale de l'Automobile) in 1950, engineers started tweaking every aspect of the car—boosting engine power, using lighter, stronger materials, and testing aerodynamics. To truly appreciate today's engineering marvels, it's insightful to look back at how the original cars were designed.
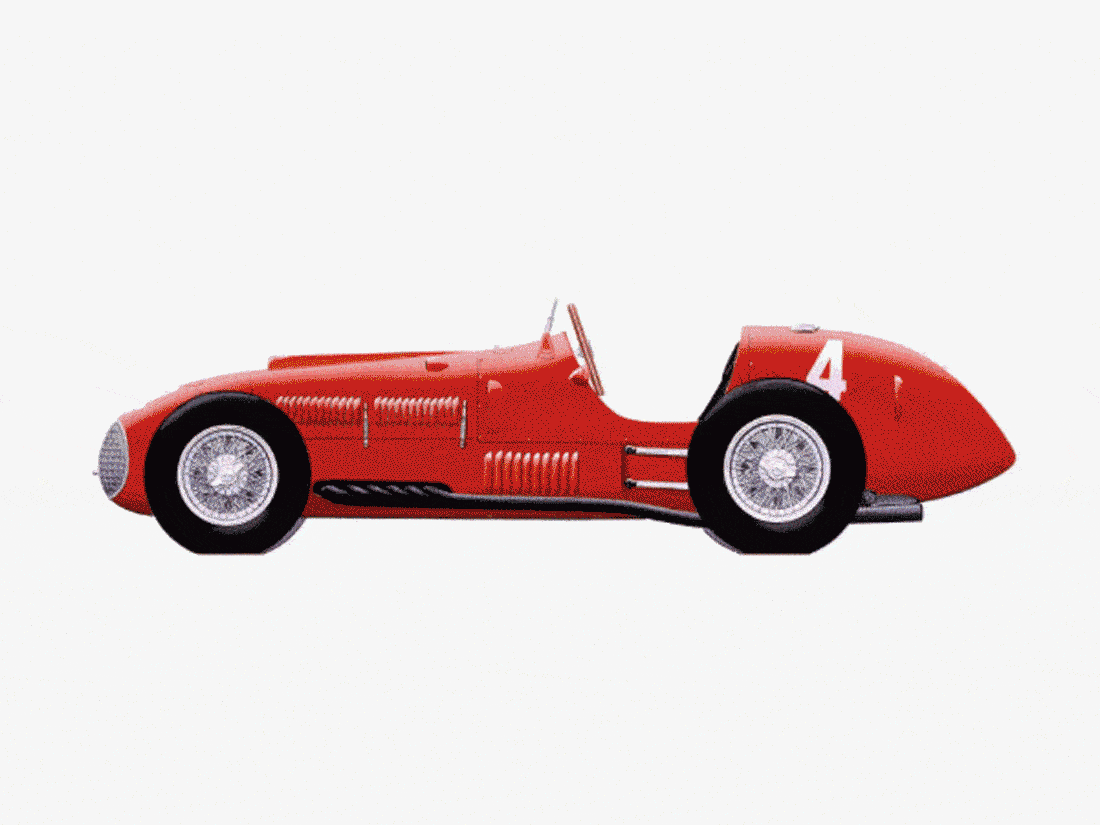
Early Years
In the 1950s, Formula 1 cars bore a striking resemblance to road cars. These early Grand Prix vehicles shared similar engine placements, sizes, and types, but were more powerful. The chassis layout, suspension, and wheel and tire sizes were often directly derived from road cars. Streamlined bodywork replaced mudguards behind tires, and passenger seats were removed to focus on performance. A driver accustomed to road cars would find the controls familiar and be quite capable of handling these early race cars. Essentially, these cars were high-performance versions of everyday vehicles, designed to push the limits of speed and endurance on the track. The cars evolved along a linear path, where the leading ideology was to achieve the highest power in the lowest-drag and weight car design possible. Aerodynamic downforce was ignored, where the primary effort went into the other four parameters governing the performance of a race car: power, weight, drag (force that slows an object down as it moves through air), and tire grip (frictional force between the tire and the road).
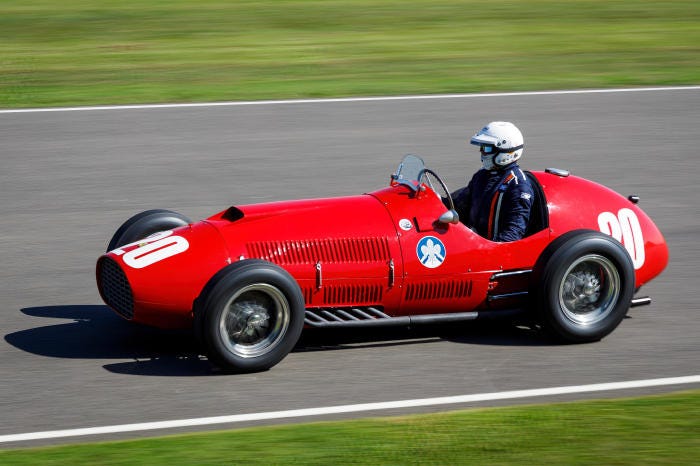
Technological Advances
The period from the 1960s to the 1980s witnessed a series of groundbreaking technological advancements that revolutionized Formula 1 from the car shown above into the car structure that closely resembles modern F1 cars.
Ground-Effect Aerodynamics
In the early 1960s, aerodynamic downforce was largely an untapped resource. Designers initially focused on reducing drag to achieve higher top speeds. Tracks from the 30’s-60’s often occurred in long straights, where the max speed could be attained over a significant distance. The introduction of aerodynamic principles, such as wings and ground effects, dramatically improved downforce allowing cars to corner at much higher speeds.
The work of innovative teams like Chaparral working with Chevrolet R&D in the Can-Am series began to shift this focus. By applying principles from aerospace, they demonstrated that generating downforce could significantly increase tire grip and cornering speeds.
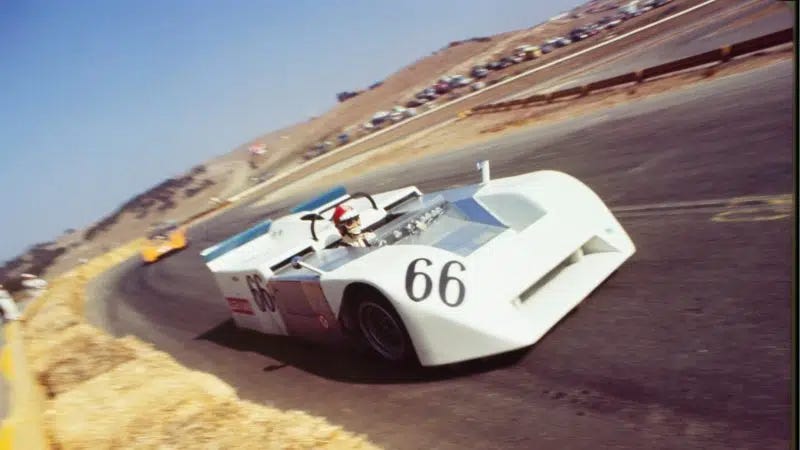
The pivotal breakthrough came with the introduction of the Lotus 78 in the late 1970s, which employed ground-effect aerodynamics. This design used side skirts and a venturi tunnel under the car to create a low-pressure area, effectively sucking the car to the track. The increased downforce allowed for much higher cornering speeds without a substantial increase in drag,
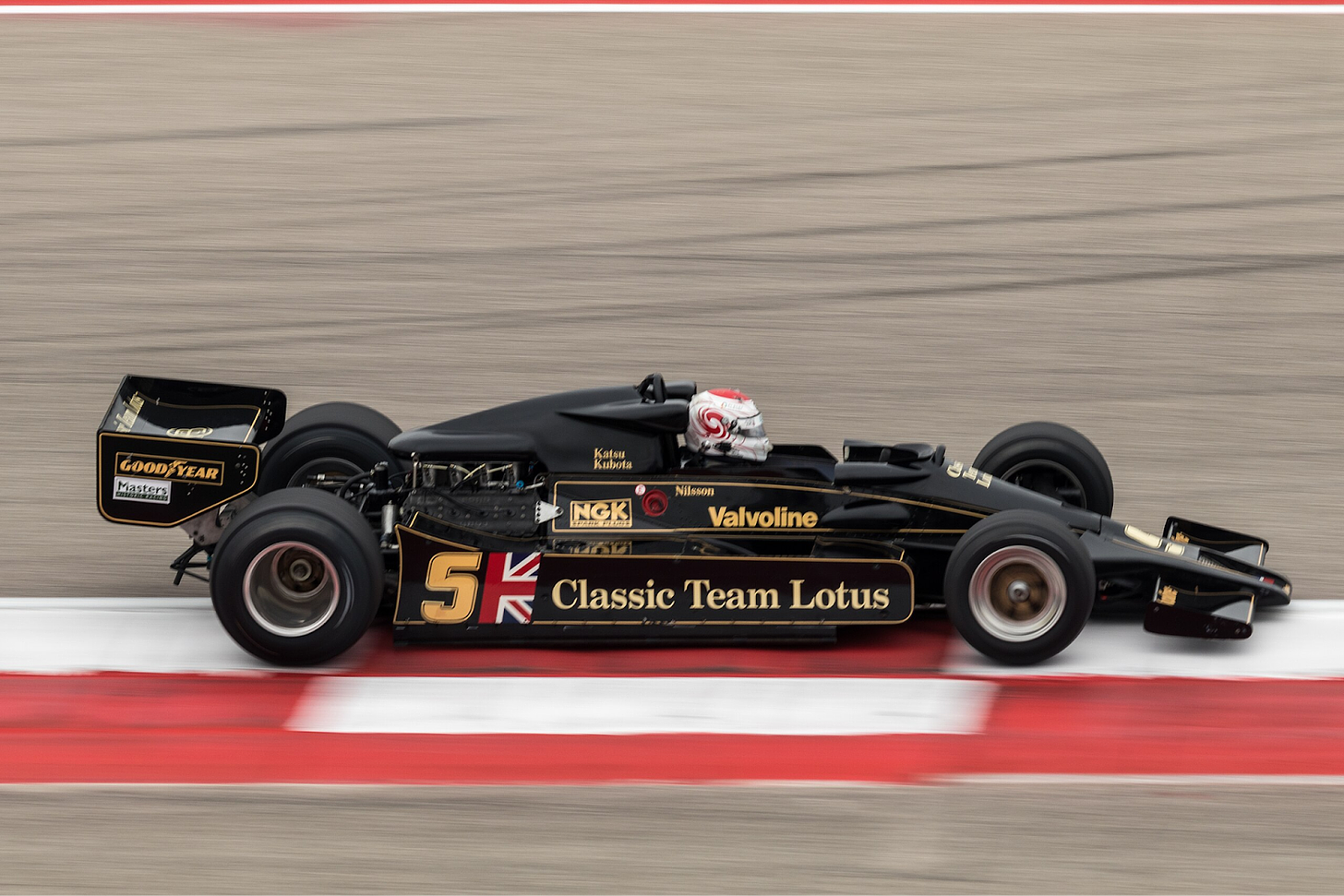
Ground Effect Explained:
High and low-pressure regions around a Formula One car create aerodynamic forces that influence its stability, speed, and handling. These pressure differences, which effectively "suck" the car to the ground, can be understood through principles of fluid dynamics, specifically Bernoulli's principle. Bernoulli’s Principle states that an increase in the speed of a fluid occurs simultaneously with a decrease in pressure.
In the context of an F1 car, air behaves as the fluid. The car's underbody, including features like Venturi tunnels, is designed to accelerate the airflow beneath the car, causing a drop in pressure. This creates a low-pressure region under the car, while the pressure above the car remains relatively higher.
The difference in pressure between the high-pressure area above and the low-pressure area below generates a net downward force known as downforce. This downforce effectively "sucks" the car towards the ground, enhancing its grip and stability. The airflow over the car’s body moves slower than the air under the car, resulting in higher pressure above and lower pressure below. The resultant pressure differential creates a downward force that increases traction by pressing the car more firmly against the track surface.
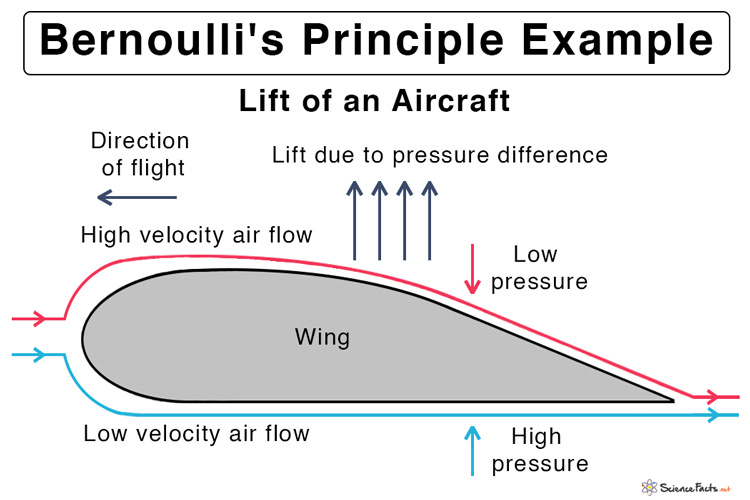
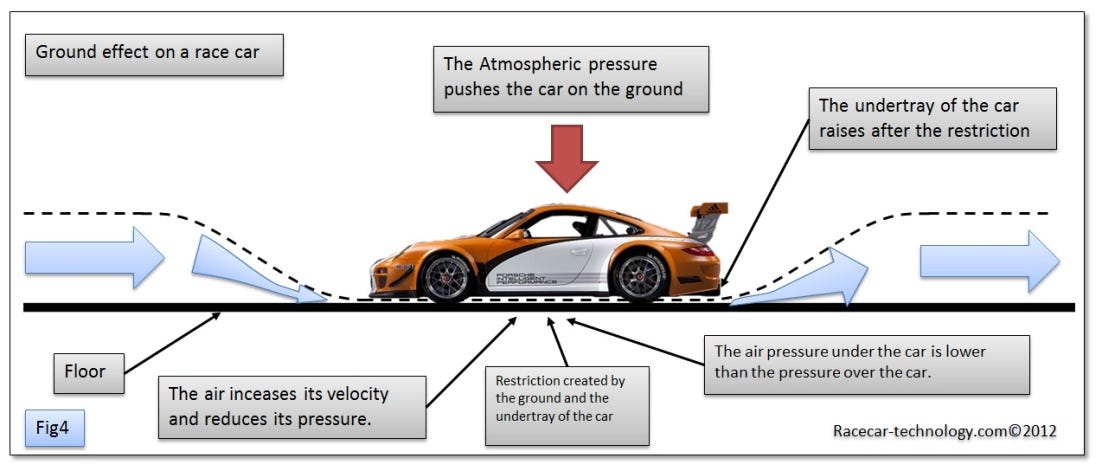
The effectiveness of ground-effect aerodynamics led teams to quickly adopt and refine these designs, resulting in cars that were not only faster but also more stable in corners. The 1980s saw the banning of side skirts and the introduction of flat floors for safety, which reduced the extremes of ground-effect but did not eliminate the fundamental principles. In 2022 with major regulation changes, ground effect designs were reintroduced by allowing sculpted floors with Venturi tunnels (tunnels that create a region of low pressure below the car).
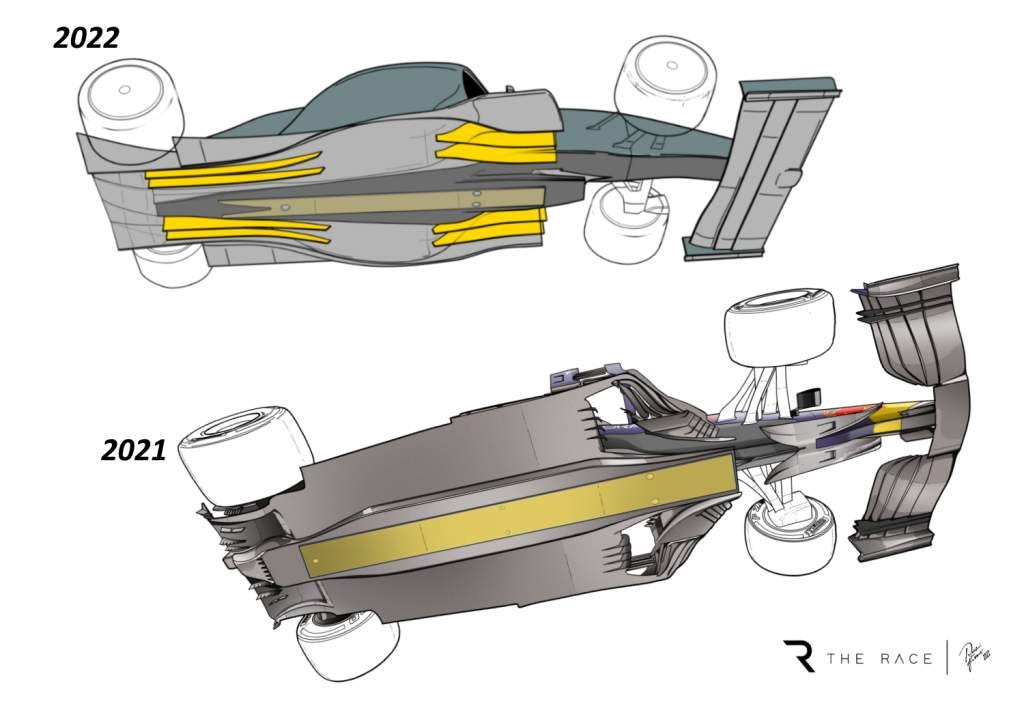
Composite Development
This era also saw the use of increasingly sophisticated materials like lightweight composites, which enhanced performance and safety. Initially, the chassis of F1 cars were constructed using riveted and bonded aluminum monocoque structures. As cars became very stiff due to the extreme sensitivity of ground-effect aerodynamics to the car's attitude (orientation/angle of car) and the height of the undersurface, the increase in suspension frequencies exposed significant structural weaknesses in the materials. This necessitated advancements in design and manufacturing.
By the early 1980s, carbon-fiber reinforced polymers (CFRP) were used in the primary structures of F1 cars. This shift was aided by advancements in the aerospace industry, which developed the necessary design and manufacturing processes. The first CFRP monocoques appeared in 1981, with McLaren and Lotus leading the way.
Lightweight composites, such as carbon fiber, have been used for the past 40 years because of their extremely high strength-to-weight ratio, which is crucial given the strict weight restrictions in F1 racing. Today, about 80-85% of a modern F1 car, by volume, is made from composites. These materials are used in various parts of the car, including the chassis, wings, bodywork, and suspension.
There’s a large number of design changes since the early years, like the introduction of computer-aided control, turbo-charged engines, and many more. The concepts above cover two of the most important developments in F1 car design.
Fundamental Principles of Race Car Performance
When we talk about Formula One performance, it boils down to five main parameters: power, weight, tire grip, drag, and downforce. These are the core elements that define a car's potential on the track. The job of a Formula One engineer is to maximize these parameters as effectively as possible, ensuring the car can perform at its peak throughout a race.
Power and Weight
The engine power and the weight of the car are two of the most straightforward yet critical aspects. The more powerful the engine, the faster the car can go. However, this power must be balanced against the car's weight. A lighter car can accelerate faster, so engineers are constantly looking for ways to reduce weight without compromising safety or structural integrity. The FIA sets strict weight limits for both the car, and the driver. Minimum dry weight including the weight of the driver is set to 798 kilograms.
Engine Design and Configuration
The core of a Formula One car's power unit is a 1.6-liter V6 turbocharged engine. This engine includes a turbocharger and hybrid electric components, with a maximum allowed RPM of 15,000 defined by current FIA regulations.
Engines are extremely complex parts, but the essence boils down to controlled explosions (gross simplification!). To understand this, we need to look at the Otto cycle, which is the foundation of how many internal combustion engines (ICE) work.
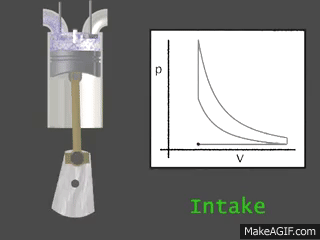
An engine operates by converting chemical energy from fuel into mechanical energy, which powers the car. The Otto cycle is made up of four stages: intake, compression, power, and exhaust.
- Intake: The cycle begins with the intake stroke. The piston moves down, creating a vacuum that draws a mixture of air and fuel into the cylinder.
- Compression: The piston moves back up, compressing the air-fuel mixture into a smaller volume. This compression makes the mixture more volatile, setting the stage for the explosion.
- Power: At the top of the compression stroke, a spark plug ignites the compressed air-fuel mixture, causing a controlled explosion. This explosion forces the piston back down, generating power.
- Exhaust: The piston moves up again, pushing the spent gasses from the explosion out of the cylinder through the exhaust valve.
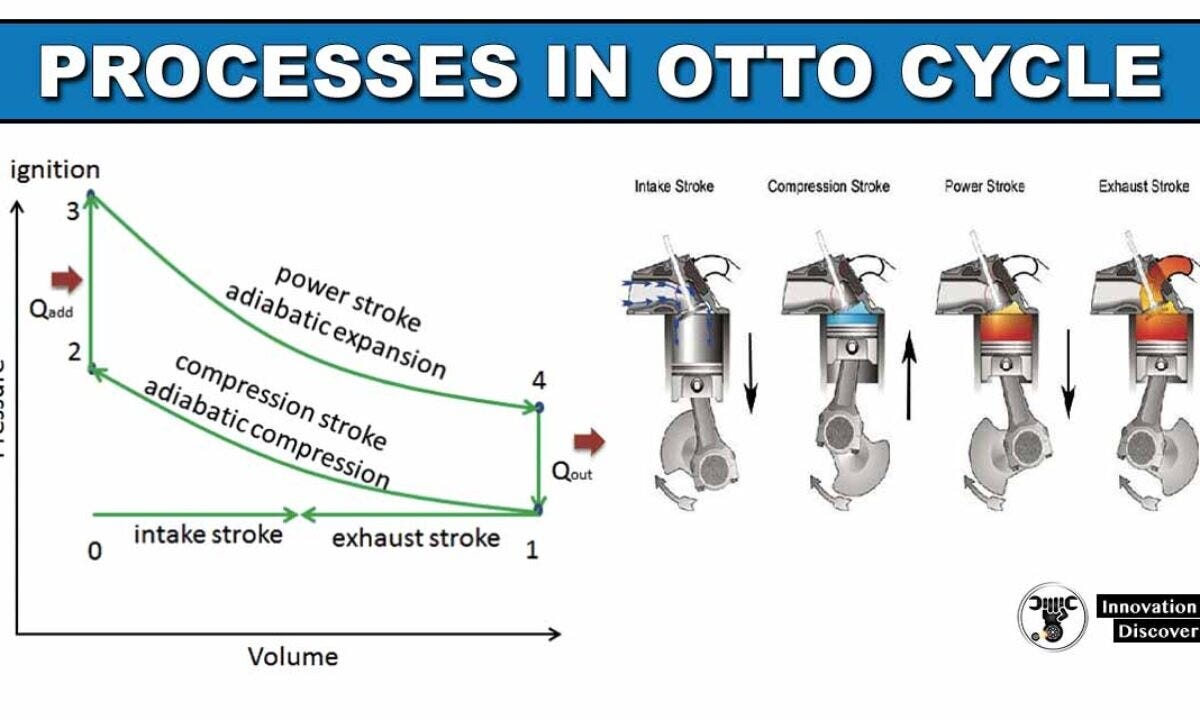
Power unit terminology can be confusing, so let's take a moment to clearly explain what each term means:
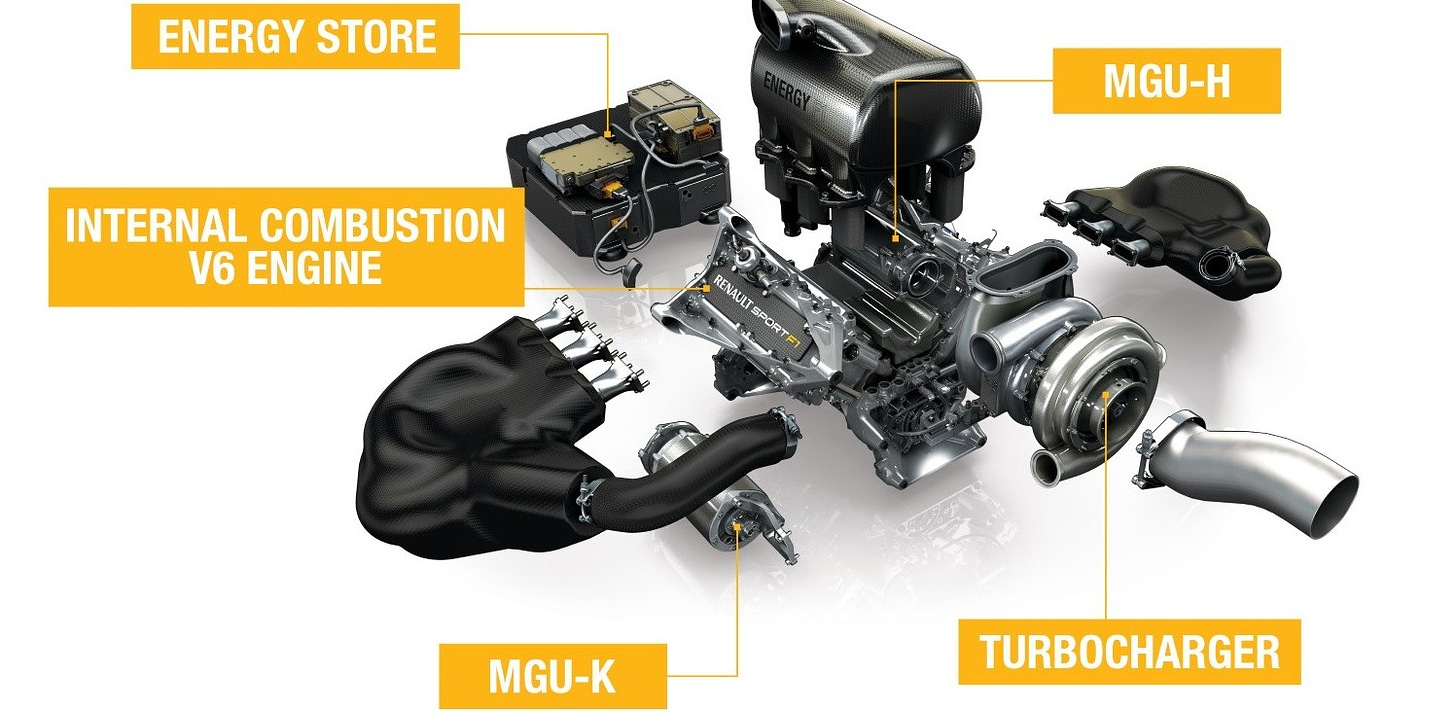
- V6 Configuration: This means there are six cylinders arranged in a V-shape, with three on each side of the engine block. Generally, more cylinders in an engine result in increased power and smoother operation. However, this also depends on other factors such as the compression ratio, engine design, and air intake systems.
- Turbocharger: A turbocharger boosts an engine's power and efficiency by forcing extra air into the combustion chamber. It has a turbine driven by exhaust gasses, which spins a compressor that increases air intake. This allows more fuel to burn, enhancing power output without adding significant weight or size to the engine.
- Hybrid Electric Systems: Consist of Motor Generator Unit-Kinetic (MGU-K) and Motor Generator Unit-Heat (MGU-H)
- MGU-K: Connected to crankshaft, recovers energy from braking and converts it into electrical energy to boost the car's power. MGU-K is connected to the crankshaft.
- MGU-H: Connected to turbocharger, recovers heat energy from the engine's exhaust gasses and converts it into electrical energy.
Read here for a more detailed overview of F1 Engine development and history.
Tire Grip
Tire grip directly influences the coefficient of friction between the tires and the track. The better the grip, the more effectively a car can transfer power to the ground and navigate turns. Managing tire wear is essential since worn tires lose grip and can dramatically affect performance.
The tractive force of a tire is generated at the contact patch, a small area where the tire meets the track. This patch is crucial for the car’s performance.
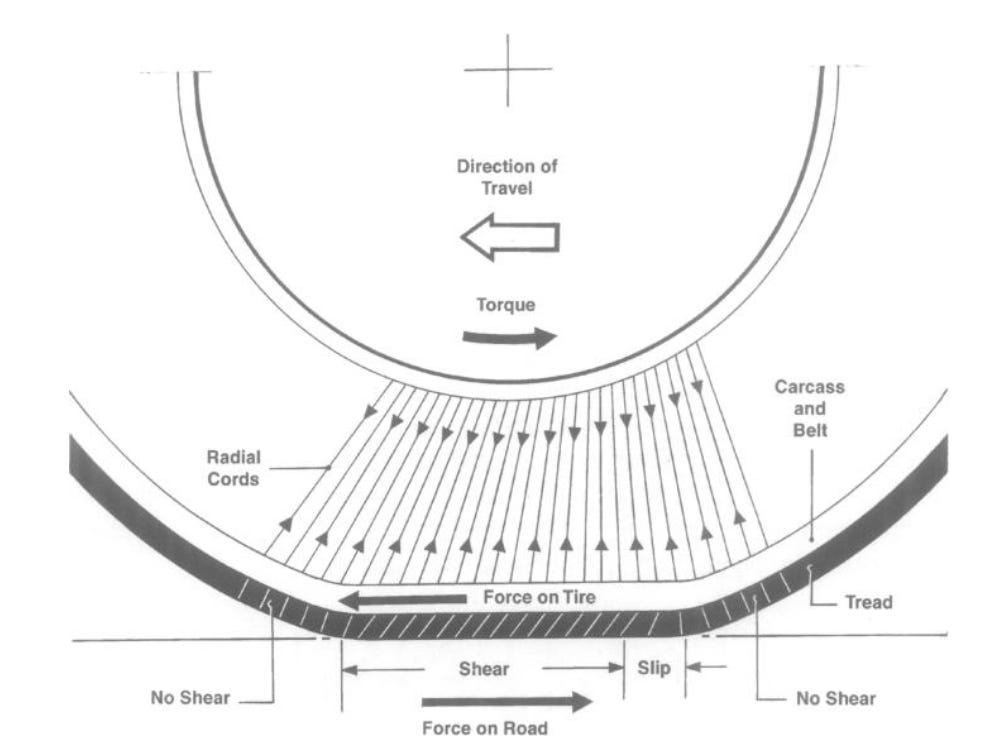
The tire tread transfers forces to the road through mechanical interlocking and molecular bonding. The rubber deforms into the road's irregularities, gripping it based on the surface detail, rubber hardness (varies with temperature), and the rubber's resistance to shearing off.
Composition:
Tires are composite structures, made from fibers like carbon, kevlar, and nylon, all bonded within a rubber matrix. The specific materials and their arrangement within the tire are carefully adjusted to achieve the desired properties. Racing tires, especially those used in Formula 1, are far more complex than regular tires. They need features like bead rings to support high loads and cords to prevent expansion under pressure.
A large part of F1 commentary revolves around the use of tires, as they play a critical role in determining race strategy, performance, and overall outcomes. The type of tire compounds chosen, their wear rates, and the timing of pit stops are pivotal factors that teams must meticulously manage. Currently, there's one supplier of tires for F1: Pirelli. Here's a breakdown of each type of tire they provide:
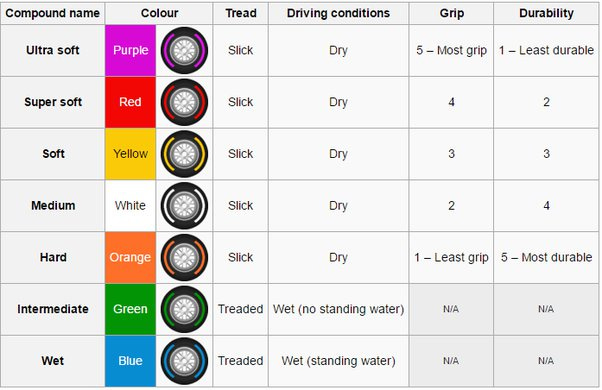
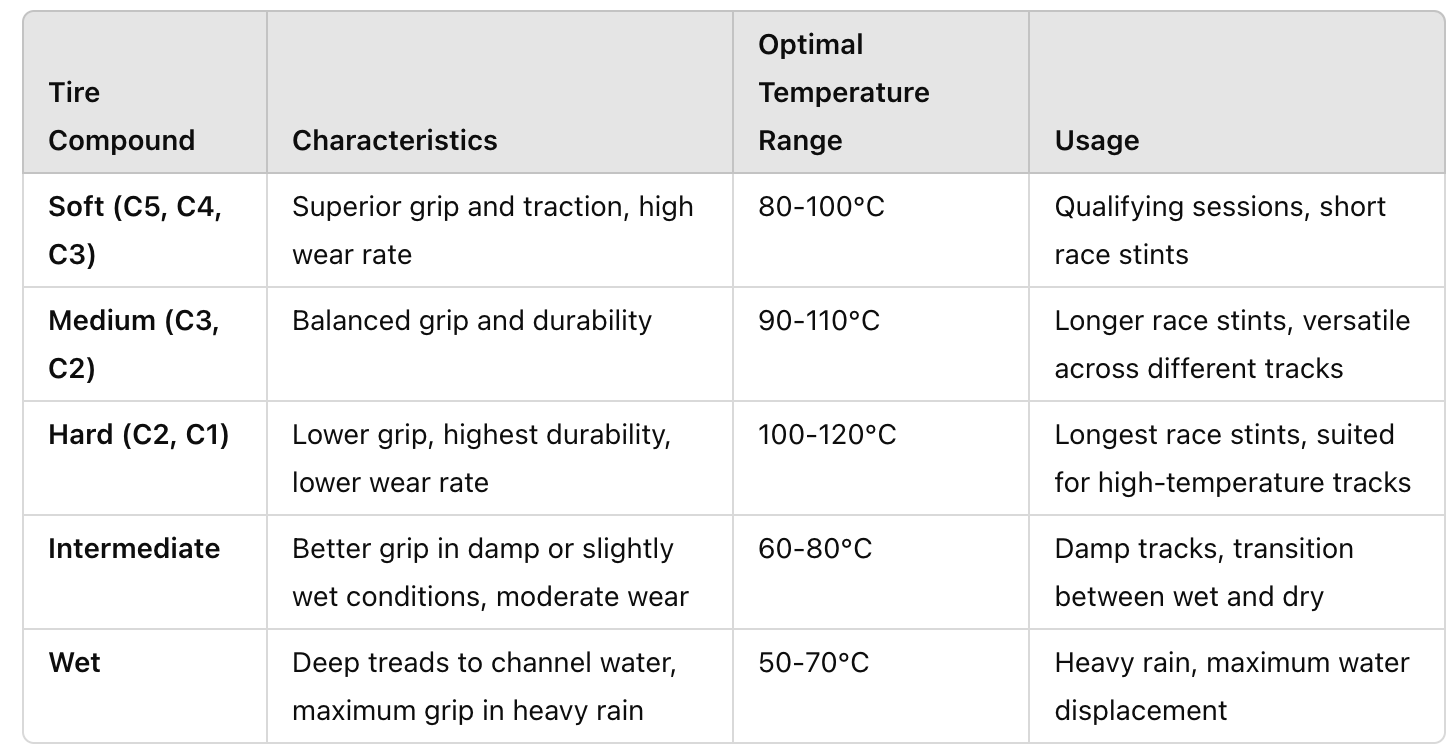
Aerodynamics: Drag and Downforce
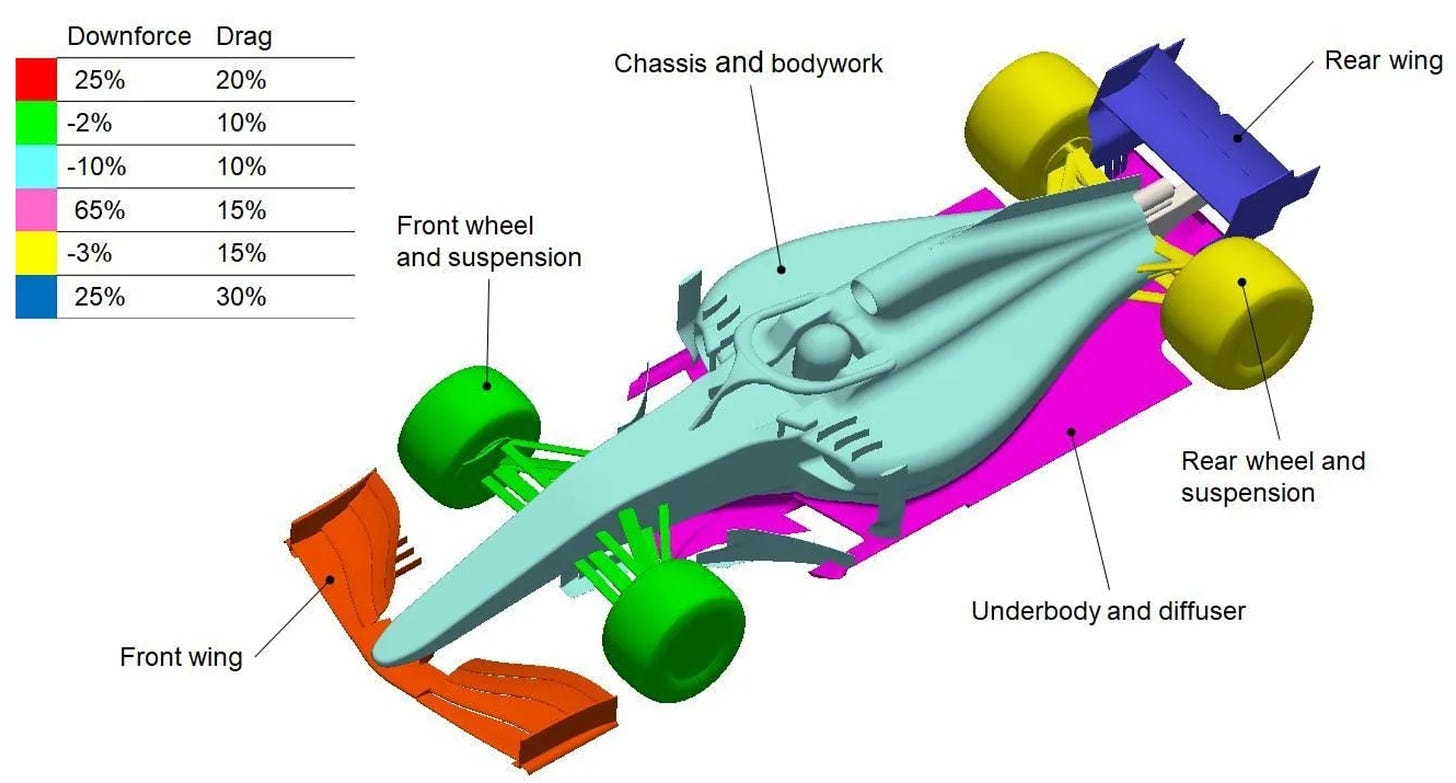
Aerodynamics plays a dual role in Formula One: managing drag and generating downforce. Drag is the resistance a car faces while moving through the air, and minimizing it is vital for achieving higher speeds. Downforce, on the other hand, is about using aerodynamic principles to push the car down onto the track, enhancing tire grip and stability, especially in corners. Simplified, the objective is to generate the maximum downforce with the least possible drag.
The importance of downforce can be seen when examining how it affects acceleration:
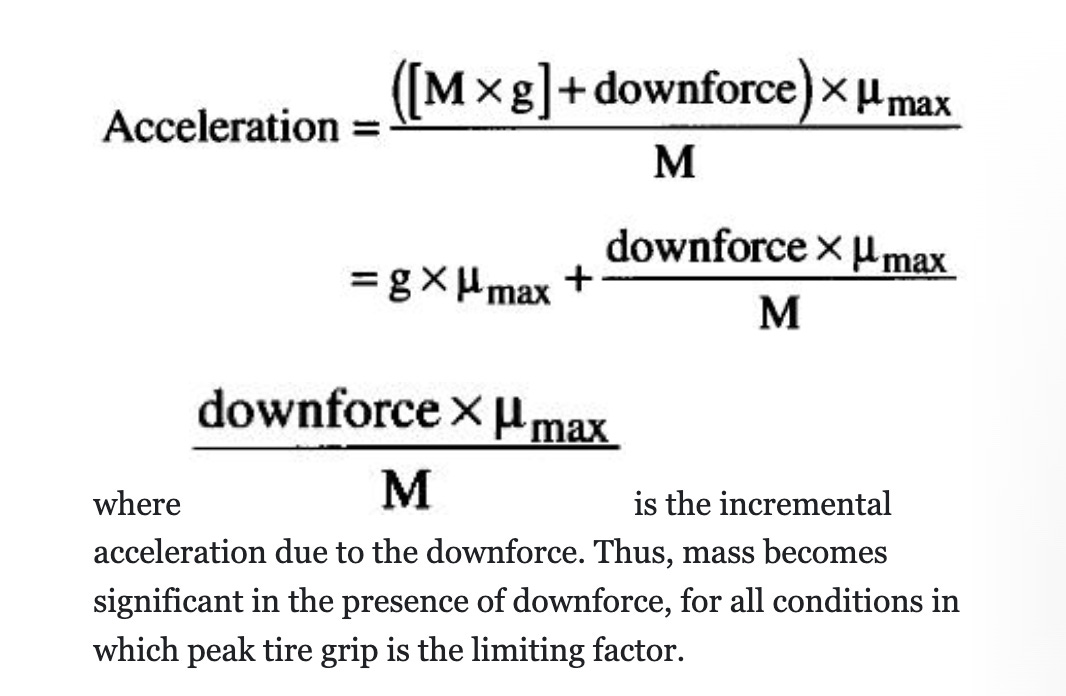
We’ve talked significantly about ground effect in sections above, modern F1 cars from 2022 use the same principle in current aerodynamic designs:
- Venturi Effect: Ground effect primarily utilizes the Venturi effect, which involves accelerating airflow through a narrow channel to create a low-pressure area. In a Formula 1 car, this is achieved by designing the underbody of the car with a shaped floor that narrows towards the rear.
- Underbody Aerodynamics: The car's underbody is shaped to create a tunnel-like structure. As the car moves forward, air flows underneath it and is accelerated through these tunnels. This acceleration reduces the air pressure beneath the car compared to the higher pressure on top, effectively "sucking" the car towards the ground.
- Front Wing: Produces 25-30% of the total downforce of the car. A two-element high-lift wing with an adjustable flap to vary the downforce obtained from the wing and hence balance the car with different rear-wing configurations.
- Rear Wing: Produces approximately 30-35% of the total downforce of the car, and approximately 25-30% of the total drag of the car.
- Diffuser: Designed to smoothly expand the accelerated air as it exits from under the car, helping to maintain low pressure, high downforce, and minimize turbulence.
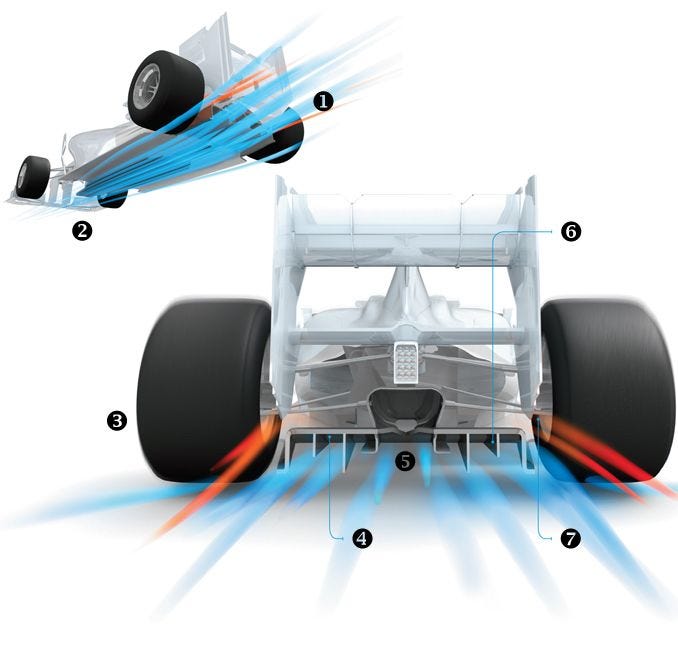
- Side Skirts: Side skirts were often used in the late 70’s/early 80’s. These skirts extended close to the ground, sealing the edges of the car and preventing high-pressure air from entering underneath, thus maintaining low pressure and high downforce. Modern regulations have banned these skirts, but other methods are still employed to harness ground effect.
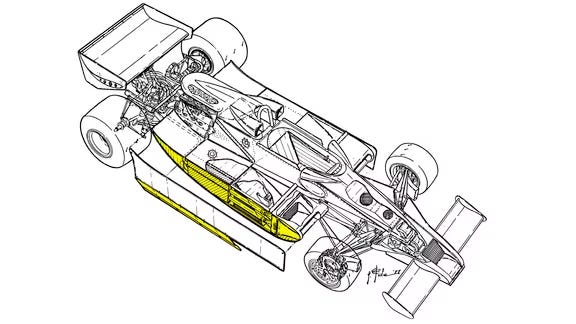
The Development Cycle of a Formula 1 Car
Creating a Formula 1 car takes about 18 months, from initial concept to obsolescence. F1 teams range in size from 300 to 1,200 people, depending on their position on the grid and the level of in-house manufacturing.
Modern F1 design teams include machinists working with metal, composite lay-out teams, aerodynamicists conducting wind tunnel models, and many more. The budget cap is set at $135 million per team, where before restrictions were placed top teams would spend up to $484 million (i.e. Mercedes, Ferrari, Red Bull)!
Development Cycle Process:
- Concept Design: The development cycle begins with the conceptual phase, where engineers brainstorm and sketch out initial designs. This phase involves extensive computational fluid dynamics (CFD) simulations to predict how the car will perform aerodynamically.
- Detailed Design: Once the conceptual design is finalized, it moves to the detailed design phase. Here, engineers create precise CAD models of every component. This phase requires close collaboration between aerodynamicists, chassis engineers, and power unit specialists to ensure all systems integrate seamlessly.
- Prototyping and Manufacturing: Formula 1 car parts are manufactured using processes such as CNC machining and composite lay-up. Teams with in-house manufacturing capabilities can quickly produce parts and iterate designs. An F1 car consists of approximately 14,500 individual components.
- Wind Tunnel Testing: Teams use wind tunnels to test scale models (50-60%) and validate their CFD simulations. Wind tunnel testing helps refine aerodynamic surfaces and optimize downforce and drag characteristics.
- Track Testing: This phase involves multiple test sessions where the car's performance is evaluated in real-world conditions. Engineers gather data on handling, tire performance, and overall reliability.
- Simulation and Data Analysis: Advanced simulators play a crucial role in F1 car development. Drivers use these simulators to provide feedback on car behavior and performance. Engineers analyze this data to make iterative improvements to the car's setup and design.
- Race-Specific Adjustments: Throughout the racing season, teams continuously develop their cars, introducing new parts and updates based on performance data from previous races. This iterative development process is crucial for maintaining competitiveness.
Watch here for an overview of Red Bull’s car development process.
Research Links:
- Formula 1 Technology by Peter Wright
- The Evolution of Formula 1 Engines by Rupesh Bhambwani